Advanced controllers for CFB Boiler
Advanced Boiler Load Controllers
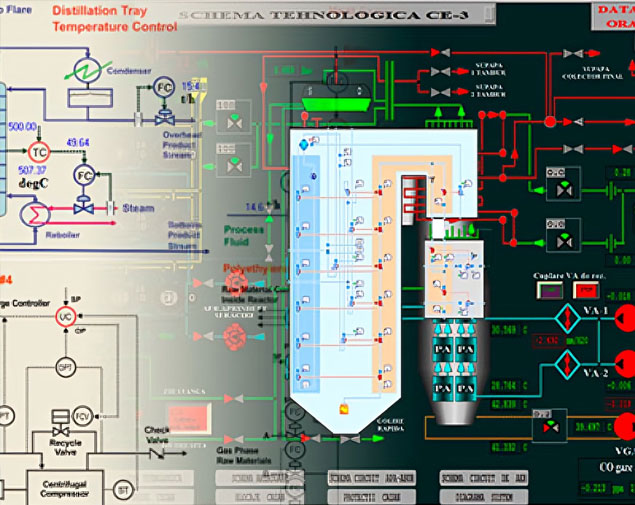
Characteristics of the Object
The specific object in this project is the Energy Boiler , with a steam production capacity of 260t/h at 100 bar. This boiler operates on a combined fuel and circulating fluidized bed, utilizing petroleum coke/coal, gas, and fuel oil as fuels. The control system overseeing this boiler is the DCS Emerson Ovation system. This setup demands a robust and adaptable control mechanism to handle the varying fuel types and maintain consistent steam production under different operational conditions.
Project Objectives:
- Automatic maintenance of generated steam pressure and load.
- Coordinated operation of the Boiler-Turbine mode.
- Automatic maintenance of the burning gas pressure before the boiler by replacing it with coke.
- Automatic regulation of emissions by maintaining the set temperature in the furnace and dosing lime into the furnace.
- Automatic calculation of the calorific value of petroleum coke fed into the furnace.
- Cascade regulator for maintaining the oxygen content in the flue gases depending on the boiler operating mode and the supplied fuel.
In the modern industrial landscape, the need for efficiency, safety, and precision in steam production is paramount.
The ISYSTEMS AUTOMATION boiler optimization solution is a sophisticated process control application was designed for the optimized combustion of circulating fluidized bed boiler. This advanced application effectively adjusts the combustion process to stabilize variations in production, fuel quantity, fuel quality, and combustion conditions, ensuring peak performance 24/7
Combustion Controller, operate as a sophisticated multi-parameter closed-loop controller, regulate multiple variables to improve combustion efficiency. In tandem, the Fuel Quality Compensator complements combustion optimization by effectively managing variations in fuel quality. This comprehensive solution eliminate fuel system disturbances caused by variations in fuel quality and quantity, thereby mitigating severe combustion instabilities.
The main control loops and logics developed for a circulating fluidized bed boiler:
- Automatic Maintenance of Generated Steam Pressure and Load: Ensuring that the steam pressure and load remain stable and within desired parameters.
- Solid fuel controls: The allocator adjusts fuel distribution based on heat values, limits, and change rates of each feeder or burner. If there's an issue with fuel feeding, the load is shifted to other feeders or fuels under automatic control.
- Steam temperature controls Utilizing cascade regulators to maintain the temperature of the generated steam by injecting feed water. The superheater model is used to predict the effect of spraying the temperature after the superheater.
- Start-up valve control
- Coordinated Operation of the Boiler-Turbine Mode: Synchronizing the operations of the boiler and turbine to maximize efficiency and performance.
- Automatic Maintenance of Burning Gas and Oil pressure/flow control (start-up burners, load burners): Managing the pressure and flow, particularly when switching between different fuels such as coke.
- Primary and Secondary Air flow controls and division
- Automatic Regulation of Emissions SO2 and NOx: Controlling emissions by maintaining the set temperature in the furnace and dosing lime to manage pollutants.
- Automatic Calculation of Calorific Value: Automatically calculating the calorific value of the petroleum coke fed into the furnace to optimize combustion.
- Adjustments to the Load Controller: Making necessary adjustments to the load regulator in response to changes in furnace temperature.
- Cascade Regulators for Boiler Drum and feedwater flow: Utilizing cascade regulators to maintain the water level in the boiler drum.
- Cascade Regulator for Oxygen Content: Maintaining the oxygen content in the flue gases depending on the boiler's operating mode and the supplied fuel.
- Bed pressure and temperature controls
- Boiler protection and burner management
- Controls of flue gas cleaning processes
Conclusion
The new system uses advanced algorithms and real-time data analysis to continuously monitor and adjust boiler settings, ensuring that the steam produced meets precise specifications.
The solution not only extends the life of equipment and components, but also provides significant cost savings in the long term.
The Operator Interface of Advanced Boiler Load Controllers:
Functionalities
- Status indicators
- Real-time status updates on boiler performance
- Alфкь and notifications for abnormal conditions
- Control adjustments
- Manual override options
- Fine-tuning of boiler settings
- Historical data access
- Logging and retrieval of past performance data
- Analysis tools for performance optimization